En Setra-buss er en veldig spesiell buss. For bak en hver Setra stilles det meget store krav til design, komfort, sikkerhet og innovativ styrke. Til dags dato legemliggjør en hver Setra visjonen og lidenskapen til pioneren Otto Kässbohrer om å bygge de mest moderne bussene i sin tid. En ting er fortsatt det viktigste for oss: den perfekte opplevelsen for sjåfører og passasjerer.
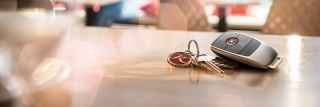
Setra Verden
Merket Setra
The Sign of Excellence.
Setra fascinerer.
Perfeksjon, estetikk, lidenskap.
Jakten på perfeksjon, kjærligheten til estetikk og vår lidenskap for det ekstraordinære gjør alle Setra-busser til en buss som oppfyller de høyeste forventningene.
Form følger funksjon.
Og mennesket følelsene sine.
Designerne våre har en helt klar oppfatning av hva som gjelder for designet til Setra. Det skal være umiskjennelig, i takt med tiden og likevel tidløst på sin helt spesielle måte. Én ting er imidlertid spesielt viktig for dem: Hver Setra skal fortelle sin egen historie gjennom designet – og på samme tid historien til merket vårt. En balansegang? Garantert. Umulig? Slett ikke.
Designerne våre er bevisst på at en buss er noe langt mer enn bare et motorkjøretøy. Den er et stykke arkitektur og interiøret et omreisende oppholdsrom. De vet også at designet må falle i smak hos helt ulike mennesker: busselskap, sjåfører og passasjerer. Derfor konfererer de før de tegner den første streken: Hvem er dagens og morgendagens passasjerer? Hvordan endres kravene deres til transport? Først da blir de første designutkastene til, og de favner vidt til å begynne med. Med digitale modeller og VR-briller blir utkastene til en sanseopplevelse fra alle synsvinkler. Etter hvert vil det være en felles favoritt som skiller seg ut i dialogen mellom alle beslutningstakere. Ut fra den kommer man til slutt frem til det endelige designet på eksteriøret og interiøret til den nye bussen.
«En buss er et omreisende oppholdsrom, et stykke arkitektur.»
En Setra vil alltid være en Setra.
Også med et individuelt tilsnitt.
Også når det gjelder design, er kunden alltid den viktigste personen for Setra. I Setra Design Center får rådgiverne våre oppfylt sine individuelle utstyrsønsker. Alle ønsker – hvor spesielle de enn måtte være – blir lyttet til. Dermed tilbys bussoperatøren et utstyrsspekter med en rekke individuelle detaljer å velge blant. Med moderne 3D-simuleringsprogrammer kan han se nærmere på kjøretøyet og teste ut varianter på en måte som ikke finnes noe annet sted. På skjermen "går" han gjennom bussen lenge før han for første gang har satt sin fot i den. Og etter all individuell tilpasning står man alltid igjen med en ekte Setra, der alt passer sammen. En buss som står for det ypperste.
Erfaring og effektivitet fordelt på 1260 meter.
Håndverkspreget produksjon med et effektivt industrielt forløp: Det høres i utgangspunktet motstridende ut, men i monteringshallen vår forenes de to elementene på harmonisk vis. For de etterlever det samme høye kravet: bygge individuelle og unike busser av beste Setra-kvalitet. På alle de 1260 meterne, lengden på monteringslinjen vår.
Ikke bare i forbindelse med designet, men også monteringen, er mindre ofte mer. Derfor strekker bare én eneste monteringslinje seg i et organisert sikksakkmønster gjennom fabrikkhallen, der de forskjelligste bussmodeller ser dagens lys. Det har helt avgjørende fordeler. Medarbeiderne sparer tid, avstander og antall grep. For hver ferdige buss beviser vi først og fremst at en høy grad av individuell tilpasning, effektivitet, fristoverholdelse og kvalitet lar seg forene perfekt på én eneste monteringslinje.
Bak det hele ligger en gjennomtenkt kjøreplan: På sin første "tur" stopper en Setra i 45 minutter på hver av rundt 50 stasjoner. Det er nok tid til at et team for eksempel får montert hele drivlinjen, det elektriske anlegget eller varme- og klimateknikken, sette inn rutene eller legge gulvet.
«På hver eneste monteringsstasjon kontrollerer vi kvaliteten på utførelsen etter strenge kriterier.»
Også når førerplassen monteres eller setene skyves på plass i interiøret, trenger det aktuelle teamet ikke mer enn tre kvarter på jobben. Alt her er håndarbeid utført av velskolerte medarbeidere – og dette inngår i tydelig definerte prosesser. Produksjon i spann med industri, erfaring i spann med effektivitet. Og ettersom medarbeiderne hele tiden utvider kompetansen, er de også velkommen på andre monteringsstasjoner. Det gjør ikke bare monteringen mer fleksibel, det gjør også arbeidet mer variert. Det styrker motivasjonen og virker positivt inn på kvalitet og feilrate. Noe som i sin tur er til glede for kundene våre. For de forventer et kjøretøy av førsteklasses kvalitet til avtalt tid.
Men det er ikke bare forløpet som sørger for kvaliteten. Også medarbeiderens høye ansvarsbevissthet bidrar til den. Dessuten kontrolleres og dokumenteres kvaliteten på arbeidet på hver stasjon. I tillegg finnes det såkalte Quality Gates etter bestemte båndsekvenser. Skulle det oppå noe som må avklares, finnes det en kvalitetskoordinator for hver stasjon.
Etter seks og en halv dag har man kommet så langt: Den nye Setra-bussen er ferdig – og medarbeiderne er stolte. Spesialister setter de tekniske systemene i drift. Motor, klimaanlegg og hele det elektriske anlegget er funksjonsklare. Etter en fullstendig rengjøring forlater den nye Setra-bussen monteringshallen og starter på siste etappe av den første turen.
Det er noe robotene aldri kan lære.
I Neu-Ulm kan vi lakkere busser i mer enn 4500 forskjellige fargetoner. Det lyder imponerende – men unikt i verdenssammenheng er noe helt annet. For det er bare hos oss at bussene lakkeres helautomatisk av roboter. Dette har mange fordeler – for kvaliteten, for vern av miljøet og for effektiviteten. Det finnes imidlertid ting som vi ene og alene overlater til våre medarbeidere og deres kompetanse. Fordi en robot aldri kan oppnå det ypperste, som vi stiller krav om.
Dette er et skuespill av det spesielle slaget. En perfekt industriell koreografi, som våre lakkeringsroboter iscenesetter rundt råkarosseriene. Den er helt unik i bussverdenen. På 13 stasjoner lakkerer robotene inntil 34 kjøretøy hver dag. De gjennomfører sin runddans jevnt og nøyaktig, programmert og overvåket av lakkerere med de strengeste krav til kvaliteten.
Tidligere påførte medarbeiderne våre lakken manuelt. Sammenlignet med dette nøyer robotene seg med ca. halvparten av den opprinnelige mengden lakk. Det senker kjøretøyets vekt og skåner dessuten miljøet.
«Teften til en aibrusher eller skriftmaler kan ingen robot i verden erstatte.»
Alt under lakkeringen følger et perfekt innstudert forløp. Etter at det nye karosseriet er grundig vasket og tørket, påfører spesialiser den gule primeren. Det neste arbeidstrinnet er et av de aller viktigste: slipingen. Og ettersom den lakkvaliteten bare blir så god som resultatet av dette forarbeidet, gir medarbeiderne våre ikke slipp på slipingen.
Først nå har roboten sin store opptreden. Strøk for strøk påfører den lakken på karosseriet. Selv om de har stor tiltro til robotene, kontrollerer spesialistene våre robotenes arbeid svært nøye. Etter hvert eneste strøk. Hvis de er tilfreds med resultatet, blir lakken tørket i tørkekammeret.
Hvor perfekte robotene enn måtte være: de er ikke kreative. Derfor har vi erfarne proffer til spesielle utformingsoppgaver. Skriftmalere, som knapt noen har noen triks å lære bort når det gjelder foliering. Og airbrush-lakkerere, som også påfører bussen innviklede design med lidenskap og stor entusiasme. Ingen jobb er for vanskelig for dem, ingen motiver er umulig. Og hver av dem har et talent som ingen robot i verden kan erstatte. De bidrar alle til å gjøre bussene våre til umiskjennelige og unike kjøretøy. På den måten viderefører de håndarbeid og høyteknologi til en helt spesiell kvalitet hos oss.
Seterundgangen for å sitte bedre.
For å sikre kvaliteten på bussetene våre setter vi noe i bevegelse. For eksempel monteringsrondellen i seteproduksjonen. Mens den dreier umerkelig rundt, fører den alltid setemontørene til rett sted til rett tid. Dit hvor det nødvendige materialet venter. Dette er svært ergonomisk siden komponentene føres ekstremt nær medarbeiderne våre. Samtidig sparer det sofistikerte systemet tid og avstand. Og det bidrar i stor grad til at kvaliteten på setene våre er så høy som den er.
Hvor bekvemt passasjerene opplever en busstur, avhenger først og fremst av setekomforten. Og den er vi særdeles opptatt av hver eneste dag. For nettopp i en Setra forventer passasjerene fullkommen komfort og avslapping. Kravene våre er minst like høye som disse forventningene. For oppholdet i en Setra skal være det første målet på reisen.
«Å reise godt vil fremfor alt si å sitte godt. Og det er vi personlig opptatt av.»
Derfor har vi i mer enn 60 år produsert passasjersetene våre selv. Og det som eneste bussprodusent i Tyskland. Dette omfatter alt fra konstruksjon til stoffbeskjæring, sying og stopping til montering. Medarbeiderne våre kjenner hemmelighetene bak best mulig ergonomi og vet hvordan perfekt stopping lages. Ved rondellen behersker hver enkelt det store variasjonsmangfoldet til Setra-setene og kan montere et komplett dobbeltsete.
Kundene våre kan tilpasse setene i tråd med egne ønsker ned til minste detalj. Det gjelder for stoffdesign og alle andre utstyrsdetaljer. Allerede fra fabrikk finnes det et mangfoldig utvalg av stoppingsmaterialer. Om ønskelig utfører vi også preging og stikksøm eller broderer en logo.
Setras seter skal imidlertid ikke bare være bekvemme og individuelle, men også vare et helt bussliv. Derfor har vi utviklet våre egne, svært strenge kvalitetskriterier. Hvert nye stoff må bestå 25 tøffe tester. Først da får det innpass i kolleksjonen vår. Og ettersom et sete også utgjør et sentral sikkerhetselement, gjennomfører vi i tillegg belastningsforsøk på armlener, håndtak og seterygger. Alt kommer kundene våre og deres passasjerer til gode. På hver eneste tur og i mange år fremover.
Tre ganger til månen.
Det er kanskje ikke viktig å komme tre ganger til månen med en buss. Men det er godt å vite at man kunne ha gjort det. Derfor er motorene våre konstruert for en kjørelengde på inntil 1,2 millioner kilometer. De produseres av Mercedes-Benz. For vi mener at den som vil bygge de beste bussene, må også utstyre dem med den beste drivteknologien som er å oppdrive.
Når vi skal utvikle en ny buss, er det først og fremst kundenes virksomhet vi fokuserer på. For Setra busser skal bidra til at foretakene klarer seg godt i den harde konkurransen. Det har mye med effektivitet og bærekraft å gjøre. Drivstoff blir stadig mer verdifullt og miljøvern stadig viktigere. Derfor er målet vårt at hver Setra skal gjøre et busselskap mer bærekraftig på lang sikt.
«Målet vårt er å gjøre motorene stadig renere og mer effektive på samme tid.»
Motorene i bussene våre spiller en nøkkelrolle. De produseres av Mercedes-Benz Motorenwerk Mannheim, der mange tekniske innovasjoner allerede inngår i serieproduksjonen. Også BlueEfficiency Power-motorene. Under videreutviklingen av disse motorene lyktes ingeniørene med noe som tidligere knapt fremstod som mulig. De er renere enn forgjengerne, samtidig som de er kraftigere, lettere og – takket være høyeffektiv forbrenning – mer sparsommelige. Dermed styrker de ikke bare totaløkonomien til bussene våre. De beviser også at miljøvern, økonomi og ytelse kan forenes på en vellykket måte.
Men lenge før vi monterer en av disse motorene i en Setra, må den først vise hva den er god for. Hver eneste en av dem. I Mannheim blir den grundig testet på en høyteknologisk prøvebenk. Helt automatisk og ned til minste detalj: Den skal til syvende og sist forflytte en Setra gjennom et helt bussliv.
I en Setra passer alt nøye sammen på drivsiden. Vi forhåndsvelger en optimal motor til hver enkelt modell ut fra det typiske bruksformålet. Og utstyrer den med en girkasse som fungerer best mulig sammen med motoren. Girkassene produseres med høy presisjon etter strenge kvalitetsretningslinjer og er absolutt jevnbyrdige med motorene med hensyn til levetid. Sammen med drivlinjene våre danner de et drømmepar for et langt bussliv. Også for totalt tre turer til månen.