Een Setra is een heel bijzondere touringcar. Want voor elke Setra gelden bijzonder hoge eisen op het gebied van design, comfort, veiligheid en innovatiekracht. Tot op de dag van vandaag belichaamt elke Setra de visie en passie van pionier Otto Kässbohrer om de modernste bussen van hun tijd te bouwen. Voor ons blijft één ding vooropstaan en dat is om chauffeurs en passagiers altijd een ultieme ervaring te bieden.
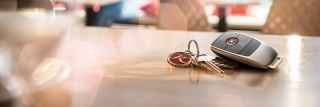
Setra World
Het merk Setra
The Sign of Excellence.
Fascinatie Setra.
Perfectie, esthetiek, passie.
Het streven naar perfectie, oog voor schoonheid en onze passie voor het buitengewone maken van elke Setra een touringcar die aan de hoogste verwachtingen voldoet.
Vorm volgt functie.
En de mens zijn gevoel.
Onze designers hebben een heel duidelijk beeld van wat Setra design inhoudt. Het moet onmiskenbaar zijn, met de tijd mee en toch op een bijzondere manier tijdloos zijn. Maar aan één ding hechten ze bijzonder veel waarde: Elke Setra moet door het design zijn eigen geschiedenis vertellen – en tegelijkertijd de geschiedenis van ons merk. Een koorddans? Zeker. Onmogelijk? Helemaal niet.
Onze designers zijn er zich van bewust dat een bus niet gewoon een auto is. Het is een stuk architectuur en het interieur ervan een rijdende kamer. Ze weten ook dat het design heel verschillende mensen moet aanspreken: ondernemers, bestuurders en reizigers. Voordat ze de eerste lijn trekken, voeren ze daarom gesprekken: Wie zijn de reizigers van vandaag en morgen? Hoe veranderen de eisen aan het reizen? Dan pas ontstaan de eerste designs, in het begin met een grote bandbreedte. Met digitale modellen en VR-brillen kunnen de ontwerpen vanuit alle hoeken worden bekeken. Geleidelijk aan komt er in de dialoog tussen alle besluitvormers een gemeenschappelijke favoriet naar voren. Dit resulteert uiteindelijk in het definitieve design voor het exterieur en interieur van de nieuwe bus.
‘Een bus is een rijdende kamer, een stuk architectuur.’
Een Setra blijft altijd een Setra.
Ook als zeer specifiek maatwerk.
Ook als het om design gaat, blijft bij Setra de klant altijd centraal staan. In het Setra Design Center realiseren onze adviseurs zijn specifieke uitrustingswensen. Iedereen, hoe speciaal ook, vindt hier een luisterend oor. Zo kunnen busondernemers kiezen uit een breed assortiment met talloze, individueel te selecteren details. Met moderne 3D-simulatieprogramma's kan hij zijn nieuwe voertuig gedetailleerd bekijken en varianten uitproberen op een manier die hij nergens anders vindt. Op de monitor “loopt” hij door de bus, al lang voordat hij voor het eerst instapt. En bij al deze individualisering staat er aan het einde altijd een echte Setra, waarbij alles bij elkaar past. Een bus die voor excellentie staat.
Ervaring en efficiëntie op 1.260 meter.
Puur ambachtelijk met een efficiënt industrieel proces: Dat klinkt misschien paradoxaal, maar in onze assemblagehal gaan beide hand in hand. Want ze streven naar dezelfde hoge standaard: individuele unieke bussen van de beste Setra kwaliteit te produceren. Op maar liefst 1.260 meter, de lengte van onze assemblagelijn.
Niet alleen bij het design, ook bij de assemblage is minder soms meer. Daarom loopt er slechts één enkele assemblagelijn in een geordend zigzagpatroon door onze fabriekshal, waarop de meest uiteenlopende busmodellen ontstaan. Dat heeft doorslaggevende pluspunten. Onze medewerkers besparen op tijd, verplaatsen en handgrepen. Maar bovenal bewijzen we met elke voltooide bus dat een grote mate van maatwerk, efficiëntie, naleving van deadlines en kwaliteit perfect op één assemblagelijn kunnen worden gecombineerd.
Hierachter zit een uitgekiende dienstregeling: Op zijn eerste reis stopt een Setra bij zo'n 50 haltes, steeds 45 minuten lang. Voldoende tijd voor een team om bijvoorbeeld de complete aandrijflijn, de elektronica of het verwarmings- en aircosysteem te monteren, de ruiten te plaatsen of de vloer te leggen.
‘Bij elk afzonderlijk assemblagestation controleren we de kwaliteit van de uitvoering volgens strenge criteria.’
Ook voor het monteren van de cockpit of het vastschroeven van de stoelen in het interieur heeft het betreffende team daarvoor niet langer dan drie kwartier nodig. Dit is allemaal handwerk van goed opgeleide medewerkers dat is vastgelegd in duidelijk gedefinieerde processen. Handwerk ontmoet industrie, ervaring ontmoet efficiëntie. En omdat de medewerkers daarbij al doende hun kundigheid uitbreiden, is iedereen ook welkom bij andere assemblagestations. Dat maakt de assemblage niet alleen flexibeler, maar de activiteit ook afwisselender. Het motiveert en komt de kwaliteit en het foutenpercentage ten goede. En dat maakt onze klanten weer blij. Want ze verwachten hun voertuig van eersteklas kwaliteit op de afgesproken datum.
Maar niet alleen het proces bepaalt de kwaliteit. Het grote gevoel voor verantwoordelijkheid van onze medewerkers draagt ook daaraan bij. Bovendien wordt bij elk station de kwaliteit van het werk gecontroleerd en gedocumenteerd. Ook zijn er na bepaalde bandgedeeltes zogenoemde quality gates. Als er tussentijds moet worden overlegd, staat er voor elk station een kwaliteitscoördinator klaar.
Na zes en een halve dag is het zo ver: De nieuwe Setra is gereed en de medewerkers zijn trots. Specialisten stellen de technische systemen in bedrijf. De motor, airconditioning en de gehele elektronica zijn dan functioneel.. Compleet gereinigd verlaat de nieuwe Setra de assemblagehal en start voor de laatste etappe van zijn eerste reis.
Sommige dingen leren onze robots nooit.
In Neu-Ulm kunnen wij bussen in meer dan 4.500 verschillende kleurtinten spuiten. Dat klinkt indrukwekkend - maar uniek in de wereld is iets anders. Want alleen bij ons worden bussen volautomatisch door robots gespoten. Dat heeft nogal wat pluspunten – voor de kwaliteit, voor de milieubescherming, voor de efficiëntie. Maar er zijn dingen waarbij we enkel en alleen op de kunde van onze medewerkers vertrouwen. Omdat een robot daar nooit de excellentie realiseert die wij aan onze standaard verplicht zijn.
Het is een bijzonder schouwspel. Een perfecte industriële choreografie die onze spuitrobots rondom de kale carrosserieën ensceneren. Deze is uniek in de wereld van de bussen. Bij 13 stations spuiten de robots zo elke dag maar liefst 34 voertuigen. Ze bewegen gelijkmatig en nauwkeurig, geprogrammeerd en gecontroleerd door spuiters met de hoogste kwaliteitseisen.
Vroeger brachten onze medewerkers de laklaag met de hand aan. In vergelijking daarmee stellen onze robots zich nu tevreden met ongeveer de helft van de oorspronkelijke hoeveelheid lak. Daardoor neemt het gewicht van het voertuig af en wordt ook nog eens het milieu ontzien.
‘Geen enkele robot ter wereld kan de intuïtie van een airbrusher of letterschilder vervangen.’
Alles in de spuiterij volgt een perfect ingestudeerd proces. Nadat de nieuwe carrosserie grondig is gewassen en gedroogd, brengen specialisten de gele vullende grondlak aan. De volgende processtap is een van de belangrijkste: het slijpen. En omdat de latere lakkwaliteit slechts zo goed is als het resultaat van dit voorbereidende werk, geven onze medewerkers het slijpen niet uit handen.
Pas nu maakt de robot zijn grote entree. laag voor laag draagt hij de lak op de carrosserie aan. Ondanks dat ze veel vertrouwen in onze robots hebben, controleren onze specialisten het werk van de robots uitermate nauwkeurig. Na elke laag weer opnieuw. Als ze tevreden zijn met het resultaat, wordt de lak in de droogkamer gedroogd.
Hoe perfect onze robots ook mogen zijn: Ze zijn niet creatief. Daarom hebben we ervaren vakmensen voor bijzondere vormgevingstaken. Letterschilders die je bijna niets meer kunt leren over folieplakken. En airbrush-spuiters die ook ragfijne designs met passie en met veel liefde voor het detail op de bus aanbrengen. Voor hen is geen job te lastig, geen motief onmogelijk. En elk brengt een talent in dat geen enkele robot ter wereld kan vervangen. Door hen allemaal worden onze bussen onmiskenbaar uniek. Zo vullen handwerk en hightech elkaar bij ons aan tot iets van een heel bijzondere kwaliteit.
Onze stoelendans rondom beter zitten.
Voor de kwaliteit van onze busstoelen zetten we het nodige in beweging. Bijvoorbeeld het assemblagerondeel van onze stoelenproductie. Terwijl het onmerkbaar draait, brengt het onze stoelmonteurs altijd op de juiste tijd op het juiste punt. Naar het punt waar precies het benodigde materiaal wacht. Dat is bijzonder ergonomisch, omdat de onderdelen extreem dicht bij onze medewerkers komen. Tegelijkertijd bespaart het geraffineerde systeem tijd en verplaatsingen. En het draagt veel bij aan het feit dat de kwaliteit van onze stoelen zo hoog blijft als deze is.
Hoe comfortabel reizigers zich voelen tijdens een busreis, hangt vooral af van het comfort van de stoelen. En daar zorgen we elke dag met veel passie voor. Want juist in een Setra verwachten reizigers het ultieme niveau aan comfort en ontspanning. Minimaal zo hoog als deze verwachtingen is ook onze standaard. Want het verblijf in een Setra moet al het eerste doel van de reis zijn.
‘Goed reizen betekent vooral goed zitten. En daar zorgen we graag persoonlijk voor.’
Daarom produceren al sinds meer dan 60 jaar onze passagiersstoelen zelf. En dat als enige busfabrikant in Duitsland. Dit omvat de bouw, het snijden van de stof, het stikken, het bekleden en de montage. Onze medewerkers kennen de geheimen van de optimale ergonomie en weten hoe perfecte bekledingen worden gemaakt. Bij ons rondeel beheerst iedereen de enorme variatie aan Setra stoelen en kan een dubbele stoel volledig monteren.
Onze klanten kunnen de stoelen tot in de kleinste details aan hun specifieke wensen aanpassen. Dat geldt evenzeer voor het design van de stoffen als voor alle andere uitrustingsdetails. Al af fabriek is er een uiterst gevarieerd aanbod aan bekledingsmaterialen. Op verzoek realiseren we ook reliëfs en doorstiknaden of naaien we een logo in de bekleding.
Maar Setra stoelen moeten niet alleen comfortabel en individueel zijn, maar ook een heel busleven meegaan. Daarom hebben we onze eigen, zeer stringente kwaliteitscriteria ontwikkeld. Elke nieuwe stoffen bekleding moet 25 taaie tests doorstaan. Pas dan mag deze in onze collectie. En omdat een stoel ook een centraal veiligheidselement is, onderwerpen we armsteunen, handgrepen en rugleuningen ook nog aan belastingsproeven. Dat komt allemaal ten goede aan onze klanten en hun reizigers. Bij elke keer en dat vele jaren lang.
Driemaal naar de maan.
Misschien is het niet belangrijk om met een bus drie keer naar de maan te gaan. Maar het is goed om te weten dat het kan. Daarom zijn onze motoren gebouwd op een afgelegde afstand van maar liefst 1,2 miljoen kilometer. Ze worden geproduceerd door Mercedes-Benz. Want wij vinden: Wie de beste bussen wil bouwen, moet ze ook de beste aandrijftechniek die verkrijgbaar is meegeven.
Wanneer wij een nieuwe bus ontwikkelen, hebben wij maar één ding voor ogen: het bedrijf van onze klanten. Want Setra bussen moeten eraan bijdragen dat bedrijven de zware concurrentie goed kunnen doorstaan. Dat hangt in grote mate af van rendement en duurzaamheid. Brandstof wordt steeds kostbaarder en milieubescherming steeds belangrijker. Daarom beogen wij dat elke Setra een busonderneming op de lange termijn duurzamer maakt.
‘Het is ons doel om de motoren steeds schoner en tegelijkertijd rendabeler te maken.’
De motoren van onze bussen spelen daarbij een sleutelrol. Ze ontstaan in de Mercedes-Benz Motorenwerk Mannheim, waar al veel technische innovaties het licht zagen. Ook de BlueEfficiency Power-motoren. Bij het doorontwikkelen van deze aggregaten is de ingenieurs iets gelukt wat eerder nauwelijks mogelijk leek. Ze zijn schoner dan hun voorgangers, maar tegelijkertijd ook krachtiger, lichter en – dankzij de uiterst rendabele verbranding – zuiniger. Daardoor maken ze niet alleen onze bussen als geheel rendabeler. Ze bewijzen ook dat milieubescherming, rendement en vermogen goed met elkaar kunnen worden gecombineerd.
Maar al lang voordat wij een van deze motoren in een Setra inbouwen, moet deze voor het eerst maximaal vermogen leveren. Allemaal stuk voor stuk. In Mannheim wordt de motor op een uiterst geavanceerde testbank in hart en nieren getest. Volautomatisch en tot in het laatste detail. Tenslotte moet deze een Setra een busleven lang betrouwbaar aandrijven.
Bij de aandrijftechniek van een Setra past altijd alles bij elkaar. Wij kiezen voor elk model aan de hand van het specifieke gebruiksdoel de optimale motor. En daarbij een transmissie die zo goed mogelijk bij de motor past. Deze transmissies worden volgens strenge kwaliteitsrichtlijnen uiterst precies geproduceerd en zijn qua levensduur absoluut gelijkwaardig aan onze motoren. Samen met onze aandrijflijnen vormen deze droomcombinaties voor een lang busleven. Ook voor in totaal drie reizen naar de maan.