La seguridad es una prioridad en Setra. La espectacular prueba de impacto pendular con el nuevo Setra MultiClass 500 LE es una muestra de ello. 1,9 toneladas de acero se lanzan contra el frontal de la MultiClass 500 LE.
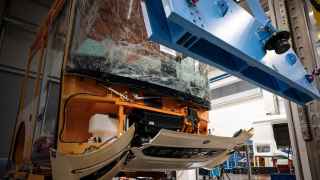
Revista SetraWorld
Todo para el conductor.
Prueba de impacto con péndulo con la Setra MultiClass 500 LE.
Todo para el conductor.
Comienza la cuenta atrás. «Tres, dos, uno»... suena por los altavoces. Suena una larga y estridente señal acústica de advertencia. Casi desde una posición horizontal, un enorme péndulo con una poderosa placa de acero se activa y golpea el frontal del autobús con un ruido ensordecedor.
Objetivo: la máxima seguridad pasiva posible.
El test se lleva a cabo en la nave de pruebas para autobuses y camiones del Centro de Desarrollo y Pruebas (EVZ) de Daimler Trucks en Wörth. La nave está llena de impresionantes bancos de pruebas y una gran variedad de cadenas, grilletes y otros amarres de los más diversos tamaños y colores. Aquí se destruyen deliberadamente vehículos, cabinas del conductor y estructuras para garantizar la máxima seguridad pasiva posible.
Entre expertos en seguridad.
El equipo de expertos en seguridad dirigido por Jörg Dünschmann, ingeniero de pruebas y responsable de la planta de pruebas se reunió in situ. Peter Schmutz y su compañero Thomas Mönnich, del departamento de pruebas de Daimler Buses, responsables de la durabilidad y la seguridad pasiva. Oguz Meric, responsable del proyecto de desarrollo de la carrocería en bruto de la Setra MultiClass 500 LE. Y por último, Bartholomäus Zak, ingeniero de ensayos y homologación de TÜV Rheinland. Este observa lo sucedido con mirada crítica y certificará la prueba, suponiendo que el resultado sea positivo.
La prueba de impacto pendular no está prescrita para los autobuses, pero, según Peter Schmutz, «para cada nueva serie de Daimler Buses garantizamos el cumplimiento de los requisitos de impacto pendular». Al fin y al cabo, la marca Setra es sinónimo de seguridad. Y a pesar del perfeccionamiento continuo de los sistemas de asistencia a la conducción, nunca se puede descartar por completo un accidente.
Con el foco puesto en la protección del conductor.
En la prueba de impacto pendular, lo importante es la protección del conductor, o mejor dicho, de su espacio de supervivencia. «Reproducimos una colisión por alcance en un camión de caja abierta», explica Jörg Dünschmann. El conductor del autobús también debe estar protegido en este escenario. Bartholomäus Zak lo expresa técnicamente: «No debe haber contacto con piezas que no se puedan retirar empujando con una fuerza máxima de 100 newtons. Estas provocarían lesiones en un accidente real».
La precisión es esencial.
Todas las inspecciones de seguridad en el EVZ se realizan estrictamente según la norma. En este caso se trata de la prueba de impacto pendular según ECE-R29.03. Para ello se requiere una precisión absoluta. La placa del péndulo pesa exactamente 1.913 kilogramos, tiene 2,5 metros de ancho, 80 centímetros de alto, y se fijó para esta prueba a una altura exacta de 4.644 milímetros.
La normativa para la prueba de impacto oscilante exige una energía de 55 kilojulios. Un julio equivale a la energía necesaria para levantar 100 gramos a un metro de altura. En este caso, hablamos de una energía 55.000 veces mayor. De ahí la necesidad de determinar con exactitud el peso de la placa y la altura milimétrica desde la que se libera. También están definidas la altura del impacto de la placa, la posición del maniquí en la zona central —que representa a una persona de estatura media— y el equipamiento completo del vehículo de prueba.
Condiciones de prueba realistas.
Se prueba la estructura de una Setra MultiClass S 515 LE, es decir, un armazón completo hasta el eje delantero incluido el parabrisas, revestimientos de la parte frontal incluyendo los faros, los grupos situados detrás, como el depósito de aire comprimido, y la puerta de acceso. En el interior se monta el puesto de conducción «Basic» completo de la nueva MultiClass 500. Estructura delantera, cuadro de instrumentos, revestimientos, volante y asiento del conductor se corresponden con el vehículo original.
Estructura detallada.
El equipo liderado por Jörg Dünschmann ha asegurado cuidadosamente esta estructura con enormes cadenas y la ha anclado firmemente al suelo. En el lado del conductor, una cinta adhesiva con un patrón en blanco y negro —conocida entre los expertos como "cinta de piano"— permite detectar cualquier posible desplazamiento de la estructura provocado por el violento impacto de la placa de acero, algo que también se registra mediante sensores. Potentes focos iluminan la estructura, junto con un conjunto de cámaras, incluidas cámaras de alta velocidad que capturan hasta 2.000 imágenes por segundo.
Durante la preparación de la prueba se respira un ambiente de trabajo profesional y concentrado. Cada movimiento está perfectamente coordinado. Para garantizar la precisión, Dünschmann verifica uno por uno todos los tornillos, cada detalle, y mide al milímetro las distancias entre las extremidades del maniquí y el puesto de conducción. “Siempre hay algo de tensión”, admite, “porque solo hay una oportunidad”. Todo se documenta cuidadosamente, y los informes técnicos se llenan con una enorme cantidad de datos numéricos.
Instancia de control independiente: TÜV.
Oguz Meric sigue el desarrollo de la prueba con expectación. Se muestra confiado, ya que “todo ha sido previamente calculado”. Sin embargo, el TÜV Rheinland, como entidad de control, exige —según explica Meric— una prueba real para poder certificar el vehículo. “Es un gran esfuerzo”, añade Peter Schmutz. Y no se refiere solo a la ejecución del test. El departamento de prototipos de la planta de Hoşdere, cerca de Estambul, fabricó expresamente la estructura, que fue transportada en camión durante unos 2.500 kilómetros hasta el Centro de Ensayos de Vehículos (EVZ), donde se sometería ahora a una prueba destructiva.
Prueba superada con éxito.
Tras un breve respiro, los expertos en pruebas y desarrollo se acercan a la estructura. Peter Schmutz abre la puerta de acceso, que permaneció cerrada durante el impacto, otro de los criterios evaluados. La primera impresión de Oguz Meric: “Tiene buena pinta”. Jörg Dünschmann lo corrobora: “Creo que todo está en orden”. En el interior, fragmentos de vidrio del parabrisas yacen sobre el suelo. Bajo la supervisión del ingeniero del TÜV, Dünschmann vuelve a medir con precisión todas las distancias entre el maniquí y el puesto de conducción.
Bartholomäus Zak, del TÜV, hace un primer balance: "Esto tiene muy buena pinta, se han cumplido todos los requisitos". Con una hoja de papel se puede verificar si hay contacto entre el maniquí y el interior del vehículo. "Es suficiente", explica, "si una hoja de papel cabe entre el maniquí y el interior. Pero aquí, seguramente caben 50 hojas". Peter Schmutz, tras el exitoso test de impacto oscilante, está seguro: "Esto le da al conductor de la nueva Setra MultiClass 500 una sensación de seguridad."
Espacio de supervivencia en la MultiClass 500 LE.
La prueba, que tiene como objetivo la protección del conductor, se realizó con dos diferentes estructuras y se superó con éxito. Estas fueron seleccionadas de manera específica para cubrir las configuraciones más críticas. Esto significa que para la MultiClass 500 LE en todas sus variantes, existe un espacio suficiente para la supervivencia del conductor.