Chez Setra, la sécurité est primordiale. L'essai spectaculaire de choc pendulaire avec les modèles 500 LE de la MultiClass en est la preuve impressionnante. 1,9 tonne d'acier frappe contre l'avant du véhicule.
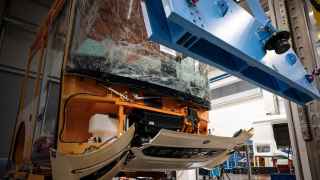
SetraWorld Magazine
Tout pour le conducteur.
Essai de choc pendulaire avec les modèles 500 LE de la MultiClass.
Tout pour le conducteur.
Le compte à rebours a commencé. « Trois, deux, un » résonne dans les haut-parleurs. Un long signal d'alerte retentit. Un énorme marteau, presque à l'horizontale, se détache maintenant avec une imposante plaque d'acier bleu clair et vient frapper l'avant du véhicule dans un vacarme assourdissant.
L'objectif : une sécurité passive maximale.
Le lieu de l'événement est le hall d'essai pour autobus/autocars et camions du centre de développement et d'essais de Daimler Trucks à Wörth. Le hall est rempli de bancs d'essai impressionnants et d'une multitude de chaînes, de manilles et d'autres dispositifs d'arrimage de différentes tailles et couleurs. Pour garantir une sécurité passive maximale, les véhicules, les postes de conduite et les torses sont délibérément détruits.
Des experts en sécurité entre eux.
Des experts en sécurité se sont réunis sur place. Il y a l'équipe de Jörg Dünschmann, ingénieur d'essai et maître des lieux de l'installation d'essai. Ensuite, Peter Schmutz et son collègue Thomas Mönnich du département d'essai de Daimler Buses, responsable de la résistance au fonctionnement et de la sécurité passive. Et également Oguz Meric, responsable du développement de la caisse nue de la MultiClass 500 LE. Enfin, Bartholomäus Zak, ingénieur en contrôle du type et homologation du TÜV Rheinland. Il observe la situation d'un œil attentif et certifiera l'essai - sous réserve d'un résultat positif.
L'essai de choc pendulaire n'est pas obligatoire pour les autobus, mais, selon Peter Schmutz, « pour chaque nouvelle série de Daimler Buses, nous nous assurons que les exigences en matière de choc pendulaire sont remplies ». La marque Setra est justement synonyme de sécurité. Et malgré le perfectionnement permanent des systèmes d'assistance à la conduite, un accident n'est jamais totalement exclu.
La protection des conducteurs au centre des préoccupations.
L'essai de choc pendulaire porte sur la protection du conducteur et plus précisément sur son espace de survie. « Nous reproduisons une collision arrière sur un plateau de camion », explique Jörg Dünschmann. Le conducteur de l'autocar doit également être protégé dans ce scénario. Bartholomäus Zak l'exprime techniquement : « Il ne doit pas y avoir de contact avec des pièces qu'on ne peut pas repousser avec un maximum de 100 Newton. Elles provoqueraient des blessures en cas d'accident réel. »
La précision est essentielle.
Tous les contrôles de sécurité dans le centre de développement et d'essais sont strictement conformes à la norme. Dans ce cas, il s'agit de l'essai de choc pendulaire selon ECE-R29.03. Une précision absolue est requise. La plaque du pendule pèse exactement 1 913 kilogrammes, mesure 2,5 mètres de large, 80 centimètres de haut et a été fixée à une hauteur de 4 644 millimètres pour cet essai.
L'énergie prescrite pour l'essai de choc pendulaire est de 55 kilojoules. Un joule est la quantité d'énergie nécessaire pour soulever 100 grammes à un mètre de hauteur. Il s'agit donc ici de 55 000 fois la quantité d'énergie. D'où le poids de la plaque calculé avec précision et la hauteur au millimètre près lors du déclenchement. La hauteur d'impact de la plaque, la position du mannequin dans la zone centrale - qui correspond à une personne de taille moyenne - et l'équipement complet de l'objet test sont également définis.
Conditions d'essai réalistes.
L'essai porte sur le corps d'un S 515 LE de la MultiClass, c'est-à-dire une ossature complète jusqu'à l'essieu avant avec le pare-brise, les habillages de l'avant, y compris les phares, les organes situés derrière comme le réservoir d'air ainsi que la porte d'accès. A l'intérieur se trouve le poste de conduite « Basic » complet de la nouvelle MultiClass 500. Le bloc avant, le tableau de bord, les habillages intérieurs, le volant, le poste de conduite – tout cela correspond au véhicule d'origine.
Une superstructure détaillée.
L'équipe de Jörg Dünschmann a soigneusement arrimé ce corps avec d'énormes chaînes et l'a solidement ancré au sol. Du côté conducteur, une bande adhésive à motifs noirs et blancs - les spécialistes parlent de bande piano - ainsi que des capteurs permettent de détecter un éventuel déplacement du torse dû à l'impact violent de la plaque d'acier. Des phares ultra-lumineux sont dirigés vers le corps, ainsi qu'une poignée de caméras, dont des caméras à haute vitesse pouvant prendre jusqu'à 2 000 images par seconde.
Une atmosphère de travail professionnelle et concentrée règne lors de la mise en place de l'essai. Tous les gestes maîtrisés. Pour être sûr, Dünschmann contrôle chaque raccordement à vis, chaque détail, mesure au millimètre près les distances de tous les membres du mannequin par rapport au poste de conduite. « On est toujours un peu tendu », admet-il, « car il n'y a qu'une seule tentative. » Tout est documenté, d'immenses données chiffrées remplissent les fiches techniques.
Une instance de contrôle indépendante : le TÜV.
Oguz Meric suit le déroulement avec attention. Il est confiant, car « nous avons déjà tout calculé ». Mais l'organisme de contrôle TÜV Rheinland exige, selon Oguz Meric, un essai réel pour la certification. « C'est un travail considérable », ajoute Peter Schmutz. Cela ne concerne pas seulement l'essai en soi. Le secteur de construction de modèles de l'usine de Hoşdere près d'Istanbul a spécialement fabriqué le torse. Il a été transporté par camion sur près de 2 500 kilomètres jusqu'au centre de développement automobile pour être testé à présent de manière destructuive lors de l'essai de choc pendulaire.
Une réussite remarquable.
Après une courte pause, les professionnels des essais et du développement s'approchent du corps. Peter Schmutz ouvre la porte d'entrée qui est restée fermée lors de l'impact, ce qui constitue également un critère. La première impression d'Oguz Meric : « Ça a l'air bien. » Jörg Dünschmann confirme : « Je pense que ça va. » Des éclats de verre provenant du pare-brise jonchent le sol à l'intérieur. Sous la supervision de l'ingénieur du TÜV, Dünschmann mesure à nouveau toutes les distances entre le mannequin et le poste de conduite.
Bartholomäus Zak du TÜV dresse un premier bilan : « Ça a l'air très bien, toutes les exigences ont été remplies ». Une feuille de papier permet de vérifier si un contact existe entre le mannequin et l'intérieur. « Il suffit qu'une feuille de papier passe entre le modèle factice et l'intérieur », explique-t-il. Mais 50 feuilles vont certainement passer entre les deux. » Peter Schmutz est certain après le succès de l'essai de choc pendulaire : « Cela donne au conducteur de la nouvelle Setra MultiClass 500 un bon sentiment de sécurité. »
Espace de survie dans la MultiClass 500 LE.
L'essai, qui vise à protéger le conducteur, a été réalisé avec deux corps différents et a été passé avec succès. Ceux-ci ont été sélectionnés de manière ciblée pour couvrir les configurations les plus critiques. Pour la MultiClass 500 LE et toutes ses variantes, cela signifie qu'il existe suffisamment d'espace de survie pour le conducteur.